3D printing with moon dust
On July 21, 1969, Neil Armstrong took his first steps on the moon – on a surface covered with moon dust. Now, 50 years later, scientists are developing technology that will make 3D printing with moon dust possible. Why? To be able to build a moon station for further space travel, without transporting heavy materials from Earth.
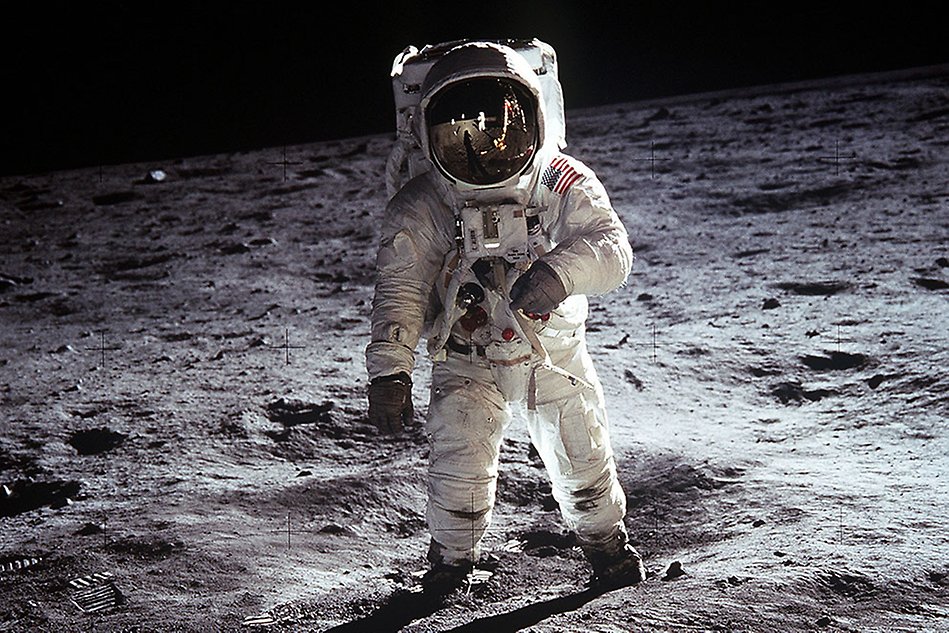
This summer marks the 50th anniversary of the first manned moon landing, when Neil Armstrong uttered the famous words: “It’s one small step for man, but a giant leap for mankind”. 1972 was the last time anyone went to the moon. The astronaut in the image is Edwin “Buzz” Aldrin. A reflection of the photographer, Neil Armstrong, can be seen in Aldrin’s helmet visor. The surface is covered in dust which potentially can be used for 3D printing building material and other components on the moon. Photo credit: NASA.
”Earth is not our final destination. Human exploration of the solar system is inevitable. There is need for innovative thinking and creative solutions to make this happen, and I hope that our research can contribute to that.”
Ross Friel
Ross Friel, Associate Professor at Halmstad University, is leading a research group working with autonomous additive manufacturing (also known as 3D printing) that can be used on the moon.
“Resources on Earth are limited and we should look beyond our planet in order to continue to thrive and survive. In space, the resources are infinite. But in order to explore our solar system and beyond, there is a need for a moon station that can function as a ‘springboard’ for further space travel. It is more economically and technically favourable to use the moon as a launch site due to its reduced gravity, no atmosphere and clear ‘skies’ in addition to the potential of using the moon’s ice for hydrogen/oxygen rocket fuel”, says Ross Friel.
Using a laser to melt moon dust
Building a moon station is not an easy task. The building material has to withstand and protect humans and scientific instruments against high energy cosmic radiation and high speed meteoroids. It is not an option to transport heavy concrete from Earth to the moon – that is untenable and far too expensive. Therefore, using already existing moon material to create durable building blocks and other useful components such as replacement parts, could be the best possible solution.
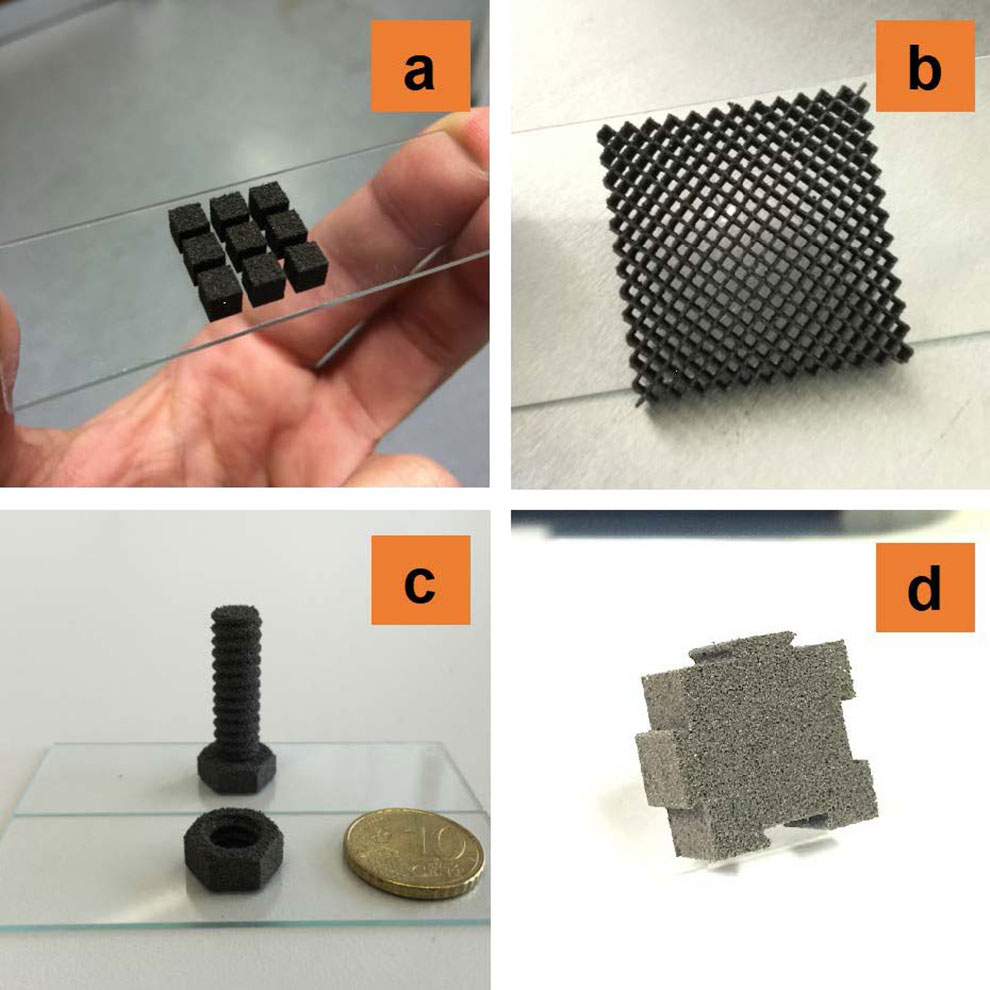
By melting a simulant, that is an Earth material that has about the same properties as moon dust, different types of structures can be 3D printed. The image shows a) dense cubes, b) a potential filter structure, c) a screw and a nut showing high accuracy control, and d) a building block in the shape of a puzzle that begins to explore the concept of creating interlocking building components for creating dense material structures directly on the moon’s surface. Photo: ROSS FRIEL
“Moon dust – the powder on the surface called lunar regolith – is a naturally occurring ceramic material. It’s a bit like volcanic ash. We have in our research used a simulant, that is Earth material with almost the same properties as moon dust. The real stuff is hard to come by!”, says Ross Friel.
Since liquid evaporates rapidly into the vacuum ‘atmosphere’ of the moon, the most promising 3D printing technology candidate for locally sourced solid matter is one that uses heat alone to melt the material. Ross Friel and his research colleagues are using a laser that exceeds 1,000 degrees Celsius to melt the moon dust.
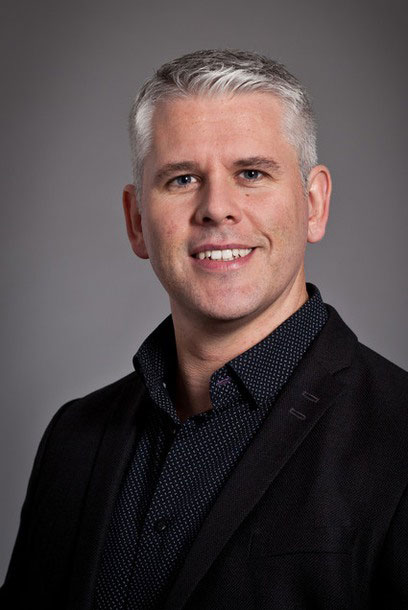
Ross Friel, Associate Professor at Halmstad University.
“A large part of our research is about how to control and optimise the laser-material interaction. The next step for us is to develop a combination of laser, solar and other heating techniques to maximise the speed and efficiency of the process when working on the moon”, says Ross Friel.
“Earth is not our final destination”
The researchers will in the coming years continue developing an autonomous 3D printing technology that will function on the moon. They will refine the testing environment so that it simulates the properties of the moon surface, for example ultra-high vacuum, and expose the printed material to, for example, radiation and impact from objects such as high velocity meteoroids.
“Earth is not our final destination. Human exploration of the solar system is inevitable. There is need for innovative thinking and creative solutions to make this happen, and I hope that our research can contribute to that”, says Ross Friel.
Text: Louise Wandel
Three questions to Ross Friel
Why did you start doing research in this field?
“I have always been fascinated by space and I hold a PhD in additive manufacturing. So, it’s a combination of my two areas of interest and expertise. What started off as a gimmick – to 3D print from moon dust – has developed into an important field of research with real potential to help make a moon base a reality.”
How did you end up in Halmstad?
“I moved to Sweden from the UK a few years ago and began working at the Max IV Laboratory synchrotron in Lund. But my wife is from Halmstad and this is where my family are, so in 2018 I was lucky enough to get an academic position and move here to Halmstad University.”
What is your favourite space movie?
“The Martian. It’s based on having to innovate to survive and is pretty realistic, mostly!”
About the research
The research group consists of:
- Ross Friel, Associate Professor at the School of Information Technology, Halmstad University, Sweden
- Athanasios Goulas, Research Associate at the School of Mechanical, Electrical and Manufacturing Engineering, Loughborough University, UK
- Jon Binner, Professor at the School of Metallurgy and Materials, University of Birmingham, UK
The type of additive manufacturing that the research group is using is called powder bed fusion. Research results were recently presented at the 2019 Future Manufacturing Technologies External link.Conference, FMTX
External link., in Malmö.
Scientific publications (2016):